Innovative air pig technology used to clean Vyrnwy Aqueduct
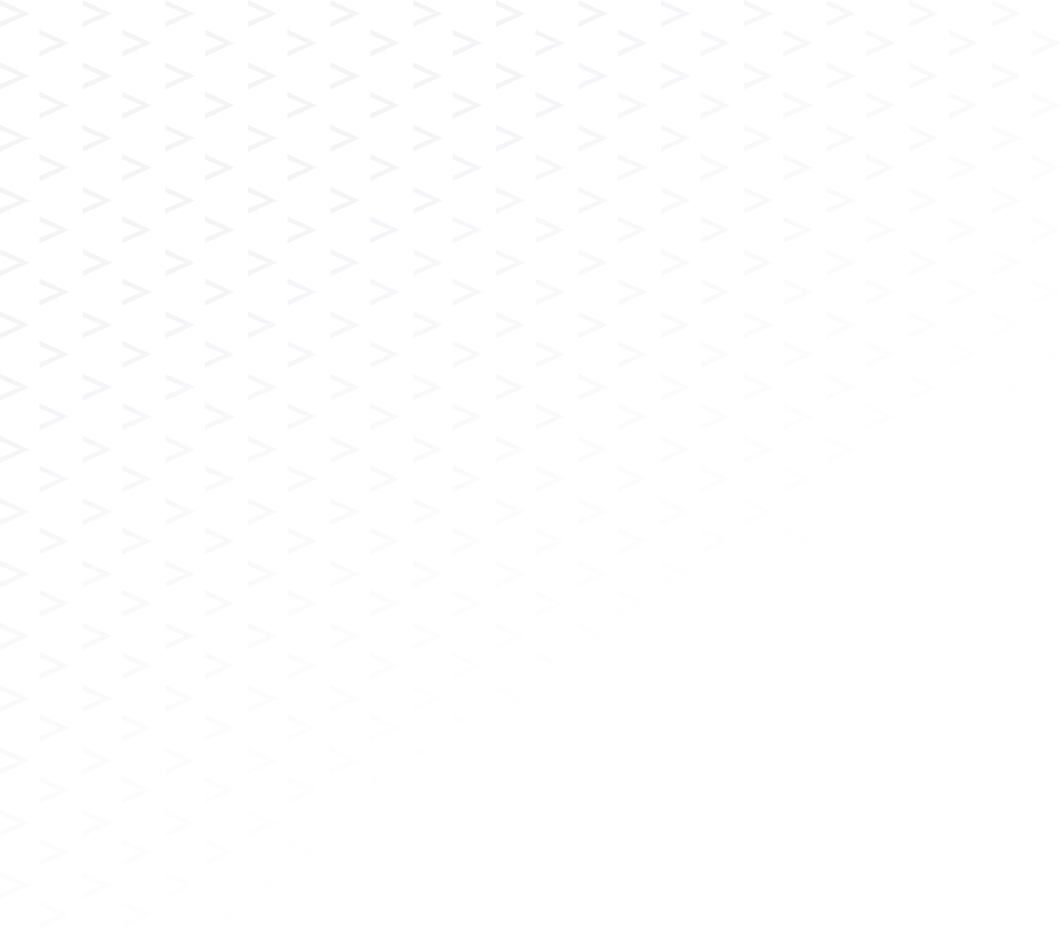
Since 1892, the Vyrnwy Aqueduct, which runs from Lake Vyrnwy through to Merseyside, has helped deliver clean wholesome drinking water to customers and communities across Cheshire, Merseyside and the North West region.
However, the pipeline now requires work to ensure the quality of customers’ drinking water and to reduce the number of water discolouration currently experienced by some customers that are supplied by the Vyrnwy Aqueduct.
The aqueduct comprises three parallel pipelines over a metre in diameter, referred to as Lines 1 and 2 (cast iron pipes) and Line 3 (steel pipe). Each line is 42 inches (over 1 metre) in diameter and has a combined distance of 139km in length between Malpas and Prescot.
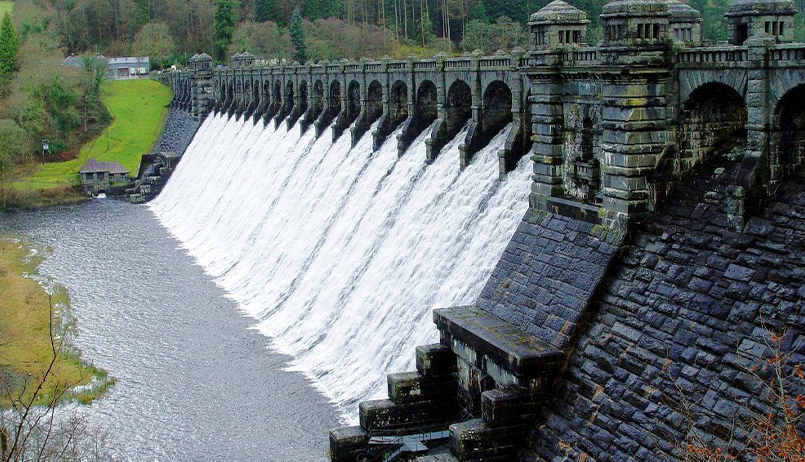
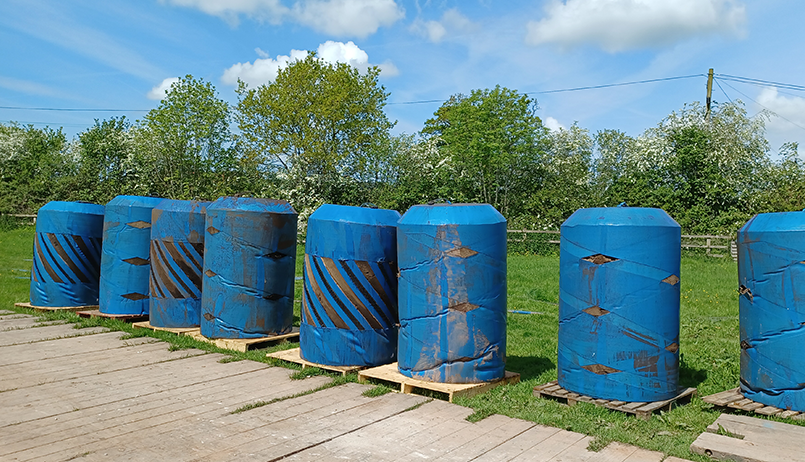
The Challenge
Over time, deposits of iron and manganese have accumulated within the aqueduct pipelines from the water running through them. These minerals don’t pose any health risks but can result in discolouration of the water and be detrimental to the internal condition of the pipe.
Due to the ages of the lines and the accumulation of minerals deposited, they now require cleaning and/or rehabilitating. In order to maintain the water supply, the refurbishment programme will be completed over a phased approach with work on the lines being carried out at different times.
The Approach
We are bringing innovative ways of working to the forefront of the industry and this project is breaking ground in how we approach the inspection, cleaning and relining of pipelines that carry water underneath Cheshire.
Due to our innovative approach to the cleaning and relining of these large-scale pipes, Avove was chosen as the contractor for modernising the Vyrnwy Aqueduct pipelines. This includes designing, constructing, testing and commissioning the three pipelines in phase 1 of the works between Malpas and Tarporley. The distance for each line is approximately 18.75km. Our approach will see a significant reduction in carbon emissions across the project.
For the cast iron lines, Lines 1 and 2, we will insert a new slighter smaller diameter plastic pipe inside the old main, creating a brand-new pipe within the host main. This process is called sliplining.
For Line 3, which is made of steel, the client originally scoped the project out using a traditional method of high-pressure jet washing. Our team of expert designers reviewed the project and recommended the use of air pig technology. This was particularly innovative because air pigging had never been used before to clean this size and length of water pipeline.
Our air pigging system utilises an air-propelled barrel-like device, known as a ‘pig’, through the 1m diameter pipes to remove any sediment that has built up from the natural minerals in the water. These ‘pigs’ are traditionally propelled by water, but our method uses air instead.
By using this technique, we have saved 1,418 tanker journeys, which has significantly reduced costs, time, carbon emissions and environmental impact, fuel, traffic congestion and noise as well as supporting road safety.
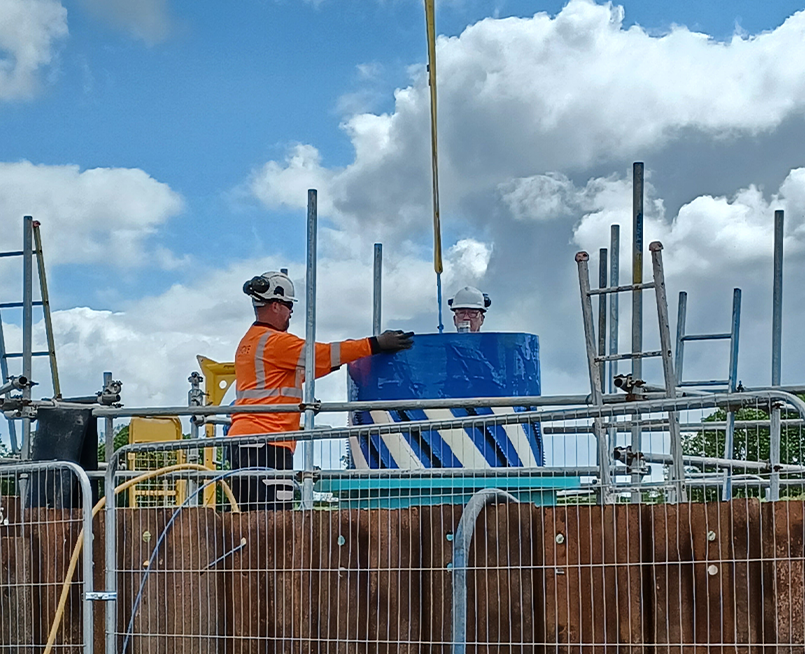
Benefits Delivered
We have brought advanced technology to the industry. Using air pigging provided a high-quality cleaning method and a host of other benefits for the project and environment, including:
- 118 tonnes of CO2 saved across the whole project
- An improved method by using close fit full contact cleaning technique
- The air pig technique cleans the pipes significantly faster, reducing the time from weeks to days example: section 1 – 2,542m completed in 4 days
- Air pigging only requires a launch and reception pit for each section – reducing the number of pits required
- Due to the speed of air pigging, defects can be assessed and repaired quickly, delivering efficiencies
- Over 15m litres of water saved compared to using traditional high pressure jetting techniques; across the whole six sections of the aqueduct
- 2,208 tanker journeys saved
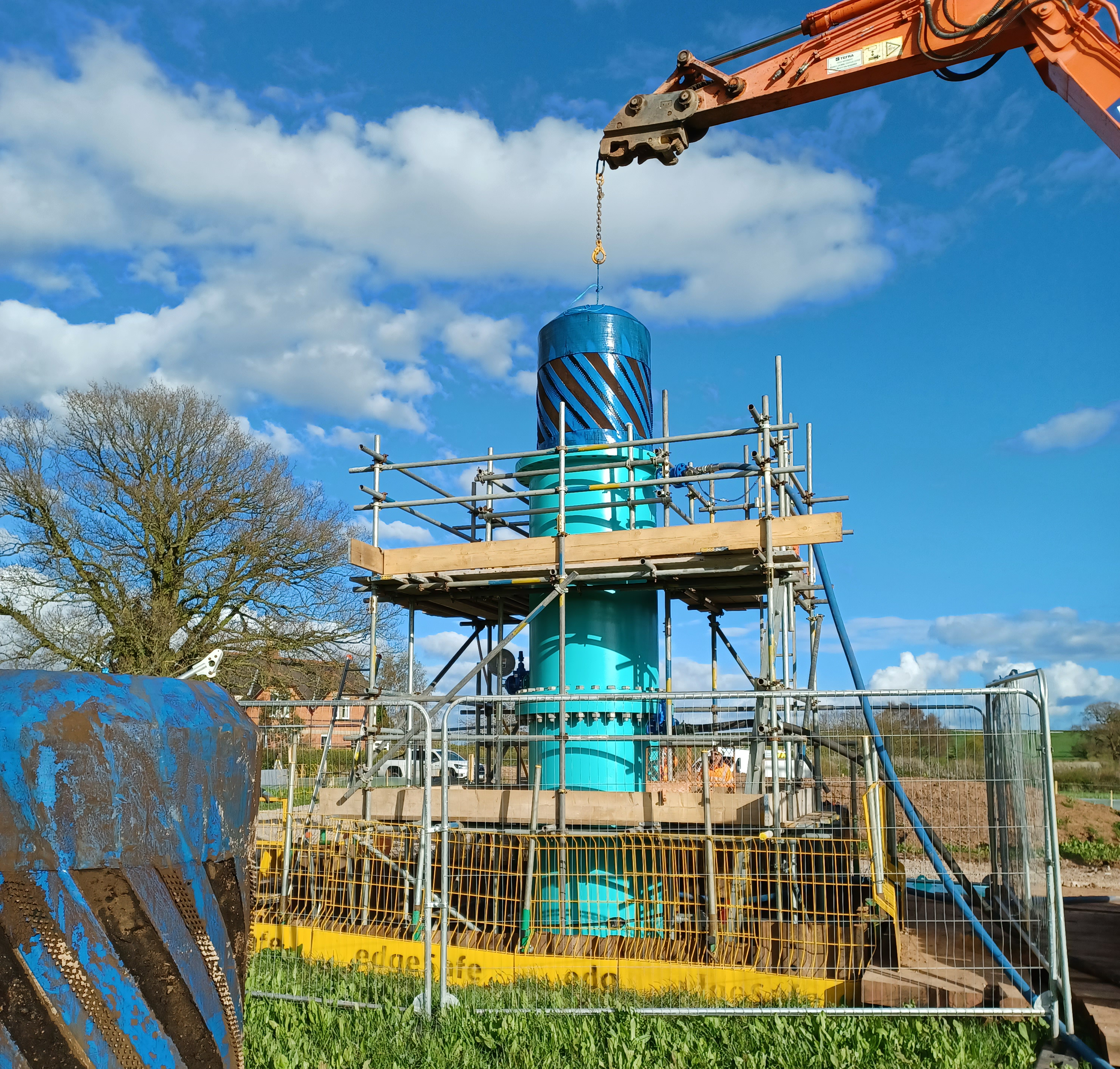
The solution
After careful planning, we designed and commissioned an effective, compliant and efficient process, that approved within the United Utilities specification C05-i2-Spec document for large diameter bitumen lined mains. Our proposal changed the cleaning method of Line 3 from high pressure jetting to air pigging.
We believe that air pigging, for this project, is safer and provides a better-quality cleaning method on a large diameter main with manganese deposits, due to the contact motion and flexible material of the pig.
We have successfully cleaned the four sections in Siphon 1, between Malpas and Tarporley, with sections 5 and 6 planned to be completed together.
The air pig system has brought a reduction of eight days in working time and reduced the number of access pits from 37 to 12. We have also seen a reduction in water usage with only one tanker movement required to bring and take away water to propel the pig instead of 1,400 tankers if high-pressure jet washing had been used.
We have mobilised the project to a very high standard and continuously strive to innovate and drive carbon reduction within our design and build aspects of the project. We are exploring potential future use of this solution and we are looking forward to completing the remaining sections with the air pig.
Innovations
- Air pigging only requires a launch and reception pit and can be carried out in six sections with one small, fixed axle tanker required for all six sections of cleaning. Each section can be air pigged in days – for example section 1 – 2,542m was completed in 4 days in total
- Air pigging propels a designed Helix pig-train down the host main with air. The Helix pigs create a vortex of water that will lift waste deposits off the internal wall. Brushing pigs and plungers can be used to remove hardened materials. Dual density swabs and pigs will not damage the existing Bitumen lining.
- The pigs are vertically launched to reduce the excavation size; where height is a concern, they can be horizontally launched. The pigs are inserted into the pipe section at ground level to reduce working at height and the pipes will then be attached to the host main.
- Our method includes the pig passing through the pipe six times
- First pass – one prover camera pig which also purged any standing water
- Second pass – first cleaning train
- Third pass – second cleaning train
- Fourth pass – third cleaning train
- Fifth pass – fourth cleaning train
- Sixth pass – one camera swab. The final camera pig acts as a final clean with a bareback swabbing of the main to provide cleanliness and will be part of the Quality Assurance procedure.
- Camera pig – we have worked exclusively with a leading supplier to develop and use a gyroscopic camera unit mounted within the pig. This will record High Definition quality footage for the main as it passes through. We will use this for both pre and post air pigging.